Chemical Dosing in Water Treatment Systems
Chemical Dosing in Water Treatment Systems
1. Introduction
In modern water treatment systems, accurate chemical dosing is essential to ensure proper purification, prevent scaling, and maintain optimal pH levels. Traditional dosing methods using mechanical flow meters often lack the precision and reliability needed for consistent performance. This is where an electromagnetic flow meter designed for small-diameter pipelines becomes an ideal solution.
2. Challenges of Chemical Dosing
Water treatment plants and industrial facilities require controlled chemical injection for:
- Disinfection (Chlorine, Ozone, etc.) : Ensuring safe drinking water by eliminating harmful contaminants.
- pH Control & Neutralization : Maintaining the correct acidity or alkalinity in industrial wastewater.
- Coagulation & Flocculation : Enhancing sedimentation and filtration processes.
Mechanical meters often suffer from clogging, wear, and inaccurate dosing, which can lead to inconsistent chemical delivery and increased operational costs.
3. The Electromagnetic Flow Meter Solution
Our compact electromagnetic flow meter offers a superior alternative by providing:
- Non-Contact Measurement : No moving parts, reducing maintenance and increasing durability.
- High Precision for Low-Flow Applications : Ideal for small-diameter dosing lines.
- Real-Time Monitoring & Automation : Integrated 4-20 mA analog output, Pulse output, and RS485 Modbus communication.
- Corrosion-Resistant Stainless Steel Body : Ensures long-term performance in aggressive chemical environments.
- Easy Installation with M12 8-Pin Connector : Simplifies integration into existing dosing systems.
4. Applications in Water Treatment Process
- Municipal Drinking Water Systems : Ensuring precise chlorine dosing for public health safety.
- Industrial Wastewater Treatment : Controlling pH levels before discharge.
- Cooling Tower Water Treatment : Preventing scale formation and corrosion through controlled chemical dosing.
5. Conclusion
By using an electromagnetic flow meter, water treatment facilities can achieve high-precision chemical dosing, reduced maintenance, and improved process control. These meters ensure efficiency and compliance with environmental regulations, making them an essential tool for any modern water treatment system.
Looking to enhance your water treatment operations? Contact us today to learn more about our high-precision electromagnetic flow meters for chemical dosing!
Related Posts
Precise pH and Conductivity Monitoring in Water Treatment Plants
In modern water treatment plants, maintaining the correct pH and conductivity levels is essential to ensure water quality, regulatory compliance, and efficient chemical dosing. Without precise monitoring, facilities may experience inefficient treatment, excessive chemical usage, and potential environmental violations. Traditional monitoring methods often lack the necessary accuracy and automation features required for modern industrial water treatment.
Optimizing Drying Processes in the Food Industry
In food production, precise humidity control plays a critical role in ensuring product quality, shelf life, and energy efficiency. Whether drying nuts, fruits, or baked goods, achieving the correct moisture level is essential for maintaining texture and flavor while preventing spoilage. Traditional humidity sensors often fail in high-temperature drying environments, making an industrial high-temperature humidity sensor a necessary solution.
pH and Conductivity Control in Industrial Cooling Towers
Cooling tower systems are essential for temperature regulation in industrial facilities, power plants, and HVAC systems. However, maintaining proper pH and conductivity levels is crucial to prevent scaling, corrosion, and microbiological growth. Inadequate monitoring can lead to equipment failures, excessive chemical use, and increased operational costs.
Efficient Liquid Level Control in Industrial Storage Tanks
In industrial facilities, accurate liquid level control is essential for operational efficiency, safety, and regulatory compliance. Storage tanks used in chemical processing, food and beverage production, and manufacturing require precise monitoring to prevent overflows, ensure consistent supply, and optimize inventory management. Traditional level sensors often struggle with reliability in harsh industrial environments, making radar level sensors the preferred choice.

Precise pH and Conductivity Monitoring in Water Treatment Plants
In modern water treatment plants, maintaining the correct pH and conductivity levels is essential to ensure water quality, regulatory compliance, and efficient chemical dosing. Without precise monitoring, facilities may experience inefficient treatment, excessive chemical usage, and potential environmental violations. Traditional monitoring methods often lack the necessary accuracy and automation features required for modern industrial water treatment.
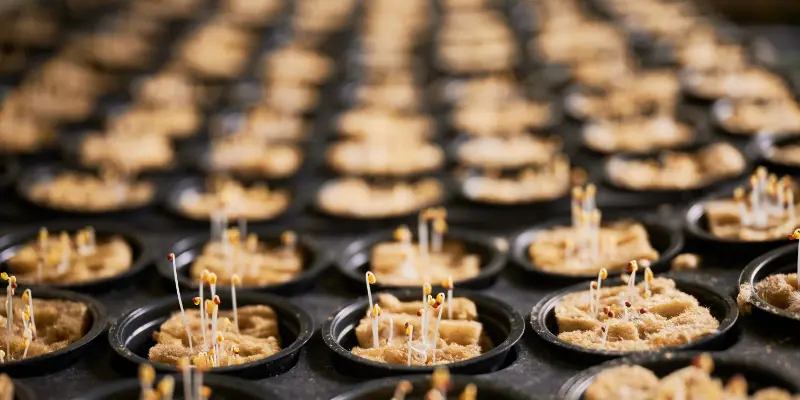
Optimizing Drying Processes in the Food Industry
In food production, precise humidity control plays a critical role in ensuring product quality, shelf life, and energy efficiency. Whether drying nuts, fruits, or baked goods, achieving the correct moisture level is essential for maintaining texture and flavor while preventing spoilage. Traditional humidity sensors often fail in high-temperature drying environments, making an industrial high-temperature humidity sensor a necessary solution.

pH and Conductivity Control in Industrial Cooling Towers
Cooling tower systems are essential for temperature regulation in industrial facilities, power plants, and HVAC systems. However, maintaining proper pH and conductivity levels is crucial to prevent scaling, corrosion, and microbiological growth. Inadequate monitoring can lead to equipment failures, excessive chemical use, and increased operational costs.
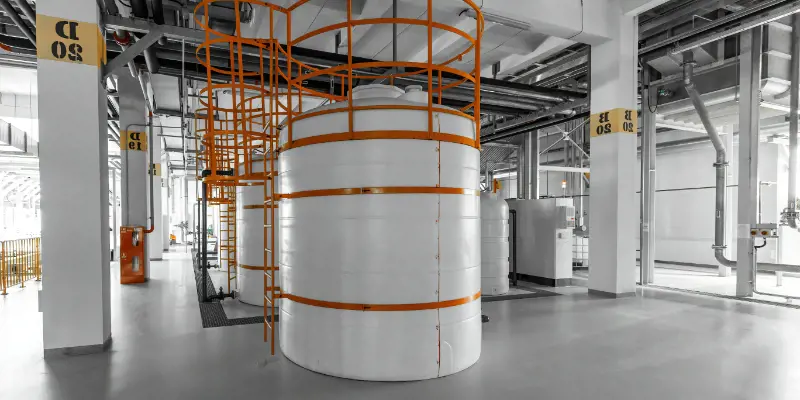
Efficient Liquid Level Control in Industrial Storage Tanks
In industrial facilities, accurate liquid level control is essential for operational efficiency, safety, and regulatory compliance. Storage tanks used in chemical processing, food and beverage production, and manufacturing require precise monitoring to prevent overflows, ensure consistent supply, and optimize inventory management. Traditional level sensors often struggle with reliability in harsh industrial environments, making radar level sensors the preferred choice.