Precise Flow Measurement in Laboratory Applications
Precise Flow Measurement in Laboratory Applications
1. Introduction
In laboratory environments, accurate and repeatable flow measurement is crucial for research, chemical analysis, and experimental processes. Traditional mechanical flow meters often struggle with small pipe diameters due to mechanical resistance and clogging, leading to inaccurate readings and frequent maintenance. This is where an electromagnetic flow meter designed for small-diameter pipes becomes an ideal solution.
2. The Challenge of Small-Diameter Flow Measurement
Many laboratory applications involve precise liquid handling, whether for titration, microfluidics, or chemical dosing. However, traditional mechanical flow meters introduce measurement errors due to moving parts that create friction and resistance. Additionally, clogging from chemical residues can cause frequent operational disruptions.
3. The Electromagnetic Flow Meter Advantage
Our electromagnetic flow meter is specifically designed for 1/4", 1/2", and 1" pipe sizes, offering superior accuracy without the drawbacks of mechanical components. Key features include:
- Non-Intrusive Measurement : No moving parts, ensuring zero mechanical wear and eliminating measurement drift.
- High Precision & Stability : Provides stable readings even for low flow rates.
- Integrated Display : Allows real-time monitoring of flow rates within the lab environment.
- Multiple Output Options : 4-20 mA analog output, Pulse output, and RS485 Modbus communication for easy integration with laboratory control systems.
- Compact & Easy Installation : The M12 8-pin connector simplifies wiring and connection, making it suitable for confined lab spaces.
4. Applications in Laboratory Settings
- Chemical Research & Analysis : Ensures accurate flow control for mixing, reaction monitoring, and chemical titration.
- Pharmaceutical Development : Supports precise liquid dosing in drug formulation and quality control.
- Microfluidics & Biomedical Research : Offers reliable measurements in low-flow applications where precision is critical.
5. Conclusion
Electromagnetic flow meters provide a highly accurate, maintenance-free solution for laboratory applications where traditional mechanical meters fail. With its compact size, digital interface, and seamless automation integration, it is the perfect choice for **small-diameter laboratory flow measurement**.
Ready to enhance your laboratory's flow measurement precision? Contact us today to learn more about our cutting-edge electromagnetic flow meter solutions!
Related Posts
Chemical Dosing in Water Treatment Systems
In modern water treatment systems, accurate chemical dosing is essential to ensure proper purification, prevent scaling, and maintain optimal pH levels. Traditional dosing methods using mechanical flow meters often lack the precision and reliability needed for consistent performance. This is where an electromagnetic flow meter designed for small-diameter pipelines becomes an ideal solution.
Precise pH and Conductivity Monitoring in Water Treatment Plants
In modern water treatment plants, maintaining the correct pH and conductivity levels is essential to ensure water quality, regulatory compliance, and efficient chemical dosing. Without precise monitoring, facilities may experience inefficient treatment, excessive chemical usage, and potential environmental violations. Traditional monitoring methods often lack the necessary accuracy and automation features required for modern industrial water treatment.
Optimizing Drying Processes in the Food Industry
In food production, precise humidity control plays a critical role in ensuring product quality, shelf life, and energy efficiency. Whether drying nuts, fruits, or baked goods, achieving the correct moisture level is essential for maintaining texture and flavor while preventing spoilage. Traditional humidity sensors often fail in high-temperature drying environments, making an industrial high-temperature humidity sensor a necessary solution.
pH and Conductivity Control in Industrial Cooling Towers
Cooling tower systems are essential for temperature regulation in industrial facilities, power plants, and HVAC systems. However, maintaining proper pH and conductivity levels is crucial to prevent scaling, corrosion, and microbiological growth. Inadequate monitoring can lead to equipment failures, excessive chemical use, and increased operational costs.
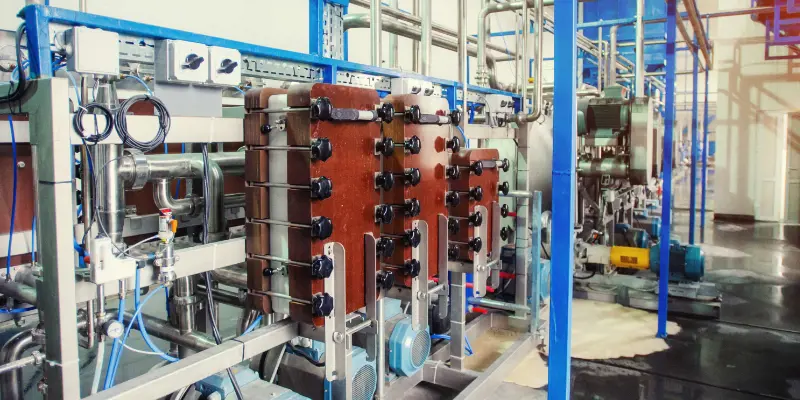
Chemical Dosing in Water Treatment Systems
In modern water treatment systems, accurate chemical dosing is essential to ensure proper purification, prevent scaling, and maintain optimal pH levels. Traditional dosing methods using mechanical flow meters often lack the precision and reliability needed for consistent performance. This is where an electromagnetic flow meter designed for small-diameter pipelines becomes an ideal solution.

Precise pH and Conductivity Monitoring in Water Treatment Plants
In modern water treatment plants, maintaining the correct pH and conductivity levels is essential to ensure water quality, regulatory compliance, and efficient chemical dosing. Without precise monitoring, facilities may experience inefficient treatment, excessive chemical usage, and potential environmental violations. Traditional monitoring methods often lack the necessary accuracy and automation features required for modern industrial water treatment.
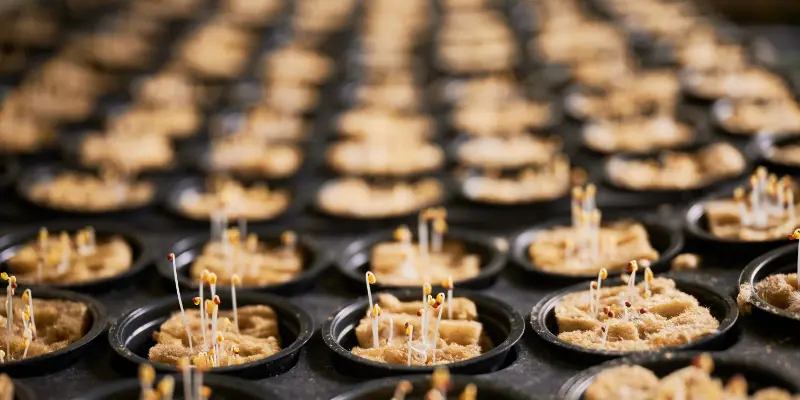
Optimizing Drying Processes in the Food Industry
In food production, precise humidity control plays a critical role in ensuring product quality, shelf life, and energy efficiency. Whether drying nuts, fruits, or baked goods, achieving the correct moisture level is essential for maintaining texture and flavor while preventing spoilage. Traditional humidity sensors often fail in high-temperature drying environments, making an industrial high-temperature humidity sensor a necessary solution.

pH and Conductivity Control in Industrial Cooling Towers
Cooling tower systems are essential for temperature regulation in industrial facilities, power plants, and HVAC systems. However, maintaining proper pH and conductivity levels is crucial to prevent scaling, corrosion, and microbiological growth. Inadequate monitoring can lead to equipment failures, excessive chemical use, and increased operational costs.